PRODUCT INFOMATION
Finishing equipment for post-processing of aluminum castings
Beer & Liquid Related Equipment
Automobile Related
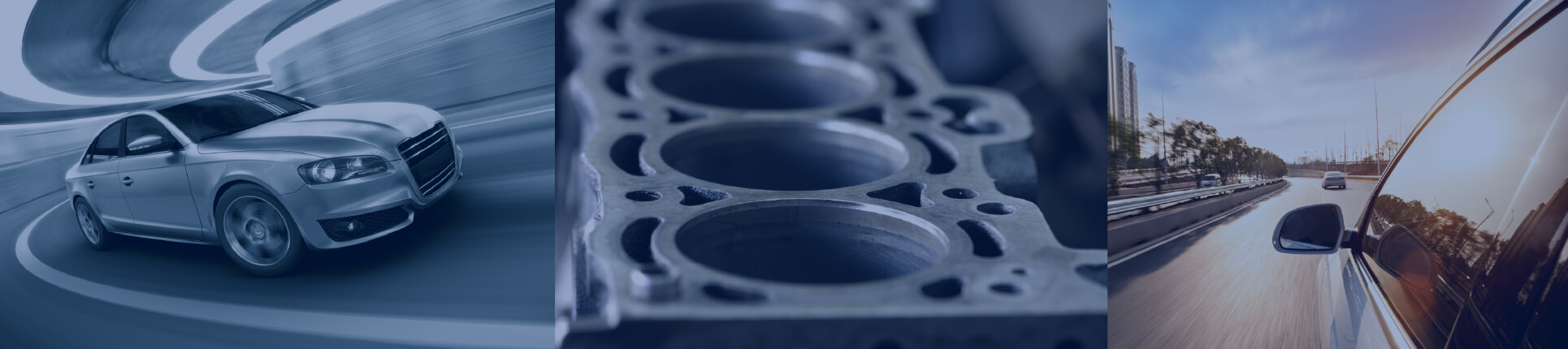
Each machine of finishing equipment
Cutting and deburring machine link system
Cutting and deburring machine link system for deburring and finishing of aluminum castings. The deburring machine employs a specialized diamond tool on a high-rigidity, high-speed spindle developed by Shiga Yamashita to achieve high-speed and highly efficient deburring and finishing.
Features
Cutting and deburring machine employing the complete Shiga Yamashita developed high-rigidity link system.
Movement on six or more axes provides flexibility to accommodate cutting and deburring of a wide variety of castings.
Shiga Yamashita has, what only a manufacturer of post-processing equipment can offer: a vast range of expertise, available to realize high levels of both utility and durability in its equipment.
Structure
Shiga Yamashita’s high-speed spindle enables speeds of 20,000 – 25,000 rpm.
The horizontal rotational axis has a function that eliminates backlash.
Jig unit | 4-axis link system |
---|---|
Cutting unit | 2-axis link system |
Cutting type | Primary cutting axis, enables high-speed spindle use |
Control panel | Space-saving design |
Console | General purpose console |
Specialized cutting equipment
Equipment for removal of sprues, dams , risers, flow-offs, and gates following casting by cutting with a toothed saw. High-speed cutting technology developed by Shiga Yamashita is employed to realize hitherto unknown cutting performance. The equipment provides for recovery and separation of filings produced by the cutting process, and is able to accommodate a wide variety of castings.
Features
Design specialized for removal of casting dams ensures extremely compact equipment.
An inverted baseplate jig enables use of a sealed structure in the design, preventing scattering of particles from the cutting process, and dramatically reducing noise.
Structure
Jig unit | Baseplate inversion system |
---|---|
Cutting unit | Raised and lowered on single axis |
Cutting method | Linear movement |
Control panel | Space-saving design |
Console | General purpose console |
Specialized deburring machine
Equipment for deburring and finishing of aluminum castings. The equipment employs a diamond tool on a high-rigidity, high-speed spindle developed by Shiga Yamashita specifically for deburring machine to facilitate high-speed and highly efficient deburring and finishing.
Features
Design specialized for linear deburring ensures extremely compact equipment.
Designed for deburring of cylinder heads in mass production applications.
Structure
Jig unit | Specialized jig |
---|---|
Cutting unit | Tri-axis orthogonal (A and B axis options available) |
Cutting method | High-speed spindle |
Control panel | Space-saving design |
Console | General purpose console |
Specialized casting sand removal equipment
Equipment used to break up and remove casting sand cores and outer molds from aluminum castings using a hammering and vibrating action. The sealed structure of the equipment is designed to mitigate the problem of dust and noise.
Features
Design specialized for casting sand removal ensures extremely compact equipment.
Superior ease of maintenance.
Structure
The drive unit employs a servo link configuration for positive transmission of vibration through accurate positioning.
Improved sealing prevents ingress of dust and sand to reduce noise and duct problems.
Jig unit | Linked retractable (accommodates work carriers) |
---|---|
Hammer unit | Link raised and lowered |
Hammer type | Pneumatic |
Control panel | Space-saving design |
Console | General purpose console |
Inverted casting sand removal equipment
Equipment used to break up and remove casting sand cores and outer molds from aluminum castings using a hammering and vibrating action. The sealed structure of the equipment is designed to mitigate the problem of dust and noise.
Features
Equipment for products such as GDC castings having large volumes of mold sand and risers.
Removal of sand is dramatically improved by placing the risers on the bottom during hammering.
Structure
The drive unit employs a servo link configuration for positive transmission of vibration through accurate positioning.
Improved sealing prevents ingress of dust and sand to reduce noise and duct problems.
Jig unit | Inverted link system |
---|---|
Hammer unit | Raised and lowered pneumatically |
Hammer type | Pneumatic |
Control panel | Space-saving design |
Console | General purpose console |
High-speed vibration casting sand removal equipment
Equipment used to break up and remove core molds from aluminum castings using high-speed vibrating action. Surpasses the concept of the conventional knock-out sand removal equipment.
Features
Strong vibration is applied to the casting by a vibration motor to break up and discharge core molds. The use of this system facilitates a significant increase in the efficiency of sand removal.
Structure
A unique high-acceleration vibration method developed by Shiga Yamashita is employed to apply strong vibration to the work to remove the sand.
Fully automatic loading and unloading.
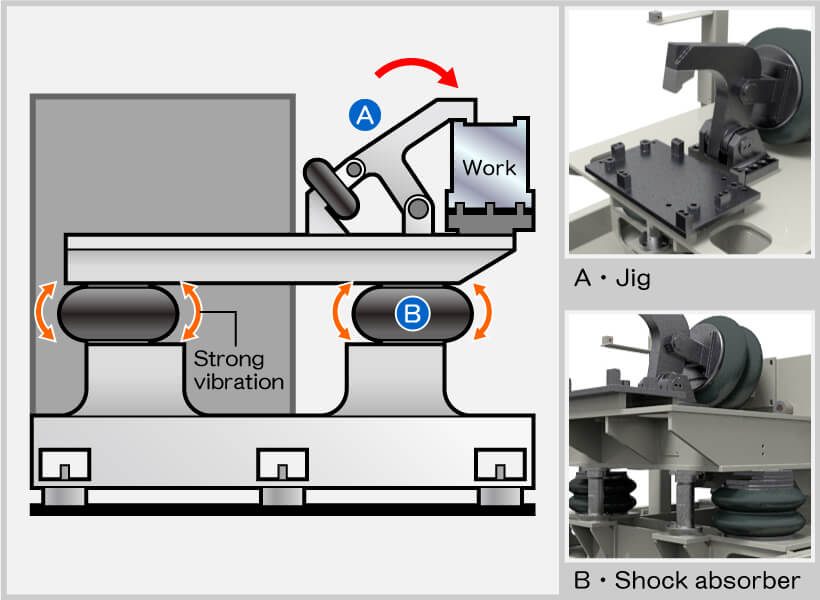
Mold-breaking casting sand removal equipment
Equipment used to break up and remove sand molds from aluminum castings using a unique pneumatic mechanism. The sealed structure of the equipment is designed with the work environment in mind to mitigate the problem of dust and noise.
Features
Designed to break up and remove outer sand molds from aluminum castings and pass only the casting onto the next process. Heat treatment following sand removal may be reduced by using this equipment in combination with a high-speed vibration machine in the next process.
Structure
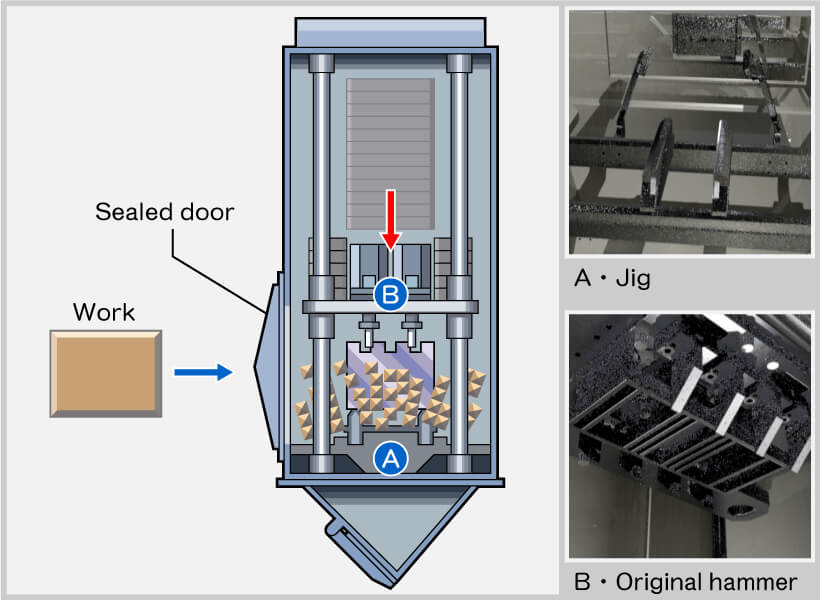
Trimming press machine
This single unit enables removal of waste from multiple surfaces and from a number of different models.
Structure
The drive unit employs a servo link configuration to improve sealing and prevent ingress of dust and sand.
Press torque control is achieved with a servomotor link to accommodate and permit control over a range of burr thicknesses.
The blade indexing mechanism accommodates the top and bottom surfaces and a number of different models, and thus enables multiple press operations within the time cycle.
The space-saving design ensures a compact configuration.
Blade unit | Servo link raised and lowered |
---|---|
Jig unit | Retractable |
Clamping unit | Auto clamping |
Control panel | Space-saving design |
Console | General purpose console |
Work carrier
High-speed transfer equipment optimized for precision transfer of heavy items under dusty conditions. Incorporates Shiga Yamashita’s own servo control and controller system.
Structure
The up-down drive employs a servo link configuration to improve sealing and prevent ingress of dust, sand, and filings.
A servo-driven rack and pinion configuration employed for horizontal movement allows high-speed with precise stopping.
The space-saving design ensures a compact configuration while enabling transfer of heavy items.
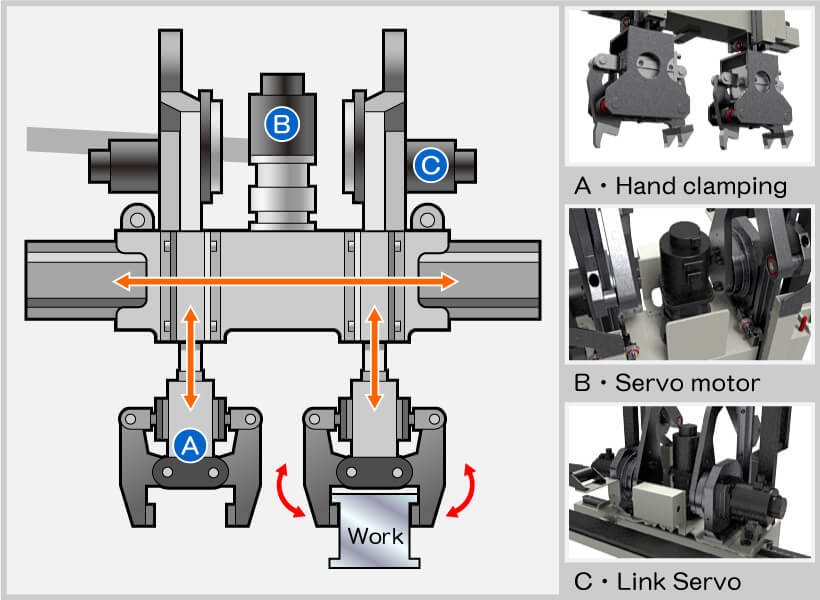
An example of a finishing equipment line
Cutting + deburring finishing line
For removal of casting dams and associated deburring on aluminum castings. The use of Shiga Yamashita’s unique Link System provides a high degree of flexibility permitting handling of castings produced by any method, provided that the casting sand has first been removed from the work. The equipment is the culmination of Shiga Yamashita’s exhaustive experience in post-processing, and as such incorporates high-rigidity, high-durability, superior utility, and a wide variety of optional functions, together with dramatically reduced maintenance requirements. For use within other equipment.
Internal machine:Cutting and deburring machine link system
Casting sand removal, cutting, and finishing line
For removal of casting sand, casting dams, and associated deburring of heavy castings characteristically employing large amounts of core sand in the casting process. The equipment is focused on sand removal, and removing the sand without a sand-baking heat treatment process. The process of removing casting dams and deburring employs Shiga Yamashita’s unique Link System to achieve a dramatic consolidation of functions.
a:Inverted casting sand removal equipment
b:High-speed vibration casting sand removal equipment
c:Cutting and deburring machine link system
Fully automatic finishing line
An integrated fully automatic high-spec line for removal of casting sand, casting dams, and associated deburring. Shiga Yamashita is able to offer what can only be offered by a specialist manufacturer, an optimum proposal based on the relevant casting product and the requirements of the customer.
a:Specialized deburring machine
b:Trimming press machine
c:Specialized cutting equipment
d:Specialized casting sand removal equipment
Casting sand removal and cutting line
A compact line for removal of casting sand and casting dams. Primarily for low-pressure castings such as cylinder heads, the compact configuration is focused on mass production and can also accommodate short cycle times.
a:Specialized casting sand removal equipment
b:Specialized cutting equipment
Deburring finishing line
A compact deburring finishing line primarily for low-pressure castings such as cylinder heads. The compact configuration is focused on mass production and can also accommodate short cycle times. Used as post-processing of D (Casting sand removal and cutting line).
a:Specialized deburring machine
Engine washing equipment
General purpose jet-type engine cleaning equipment
Washing equipment for removal of cuttings and filings following machining of items such as automobile cylinder heads, cylinder blocks, and transmissions.
Features
A completely new type of washer employing an overhead conveyor.
Configured for washing and draining in separate tanks.
The need for conventional targeted washing is eliminated by the effective switching between jet washing, direct impingement washing, and rapid drainage, thereby enabling use with a wide range of work-pieces.
Shiga Yamashita is able to provide the optimum washing system through a combination of models, time cycles, and washing accuracy.
※ Ten related patents have been granted.
Option specification
This innovative unit performs locally targeted washing and blowing within a preset cycle time by inserting a numerically controlled nozzle in crucial processed holes.
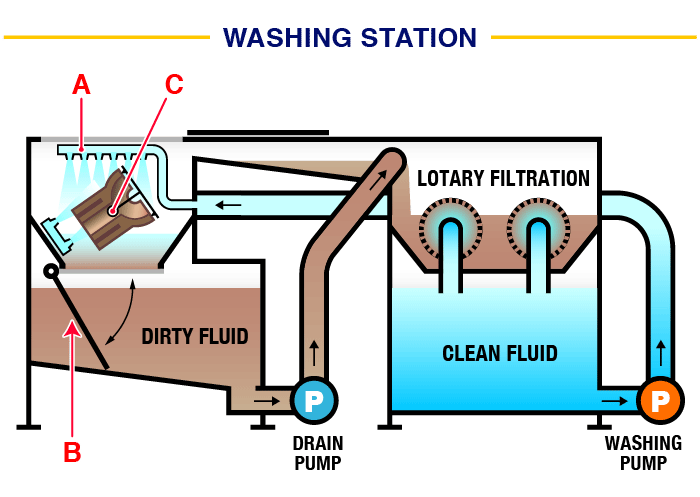
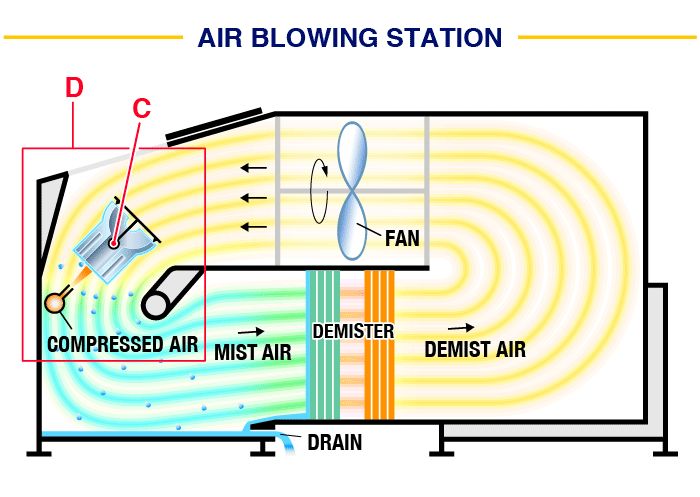
CYCLE TIME & ST QUANTITY | We can respond flexibly by user spec. |
---|---|
BASE WASHING PRESSURE & FLOW | 8〜10MPa×1000L/min |
FILTRARION SYSTEM | ROTARY FILTRATION TYPE (CIGA) |
WORK TRANSFER TYPE | LODER TRANSFER SYSTEM (CIGA) |
WORK DELIVERY | CONVEYOR(We can respond flexibly by user spec) |
LAYOUT | We can respond flexibly by user spec. Please consult. |
SYSTEM CONTROLLER | SYNC-21A・PLC functional standard built-in (CIGA) |
SERVO MOTOR | Y.E(Please consult to charge of our company about detailed spec) |
Hybrid-type engine cleaning equipment
Washing equipment for removal of cuttings and filings following machining of items such as automobile cylinder heads, cylinder blocks, and transmissions.
Our revolutionary washing/blowing equipment allows you to perform washing, draining and air-blowing with a single machine unit.
Features
The small space saving equipment allows you to perform washing and blowing within the same limited space. The high-precision washing function makes full use of jet washing and quick draining capabilities, and the blowing function makes full use of the air volume and flow rate provided by the blower fan. Our innovative equipment also excels in noise suppression and energy saving.
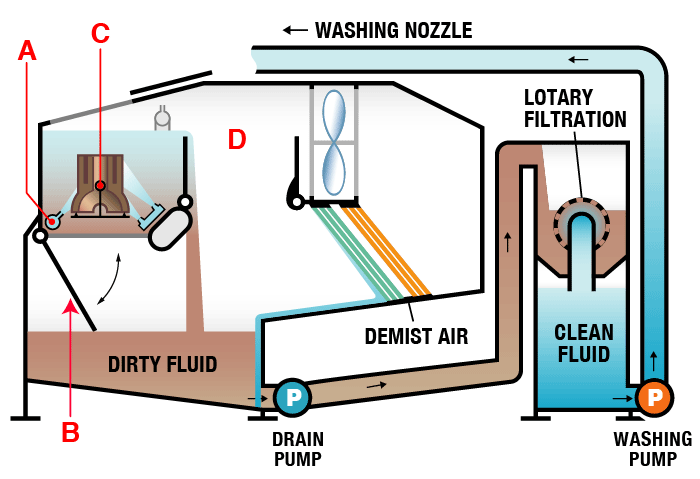
B. QUICK DLAIN DAMPER
D. HYBRID TYPE BLOWING SYSTEM
※ Ten related patents have been granted.
Hybrid-type engine cleaning equipment for large work
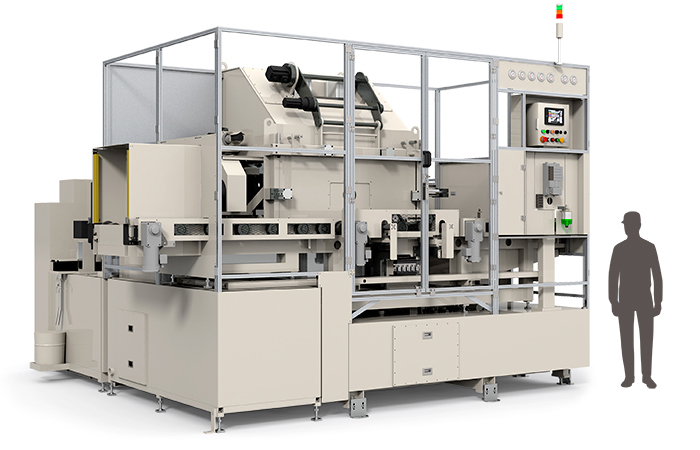
※ Please contact us for specs.
Finishing equipment line for setting by hand
<Internal machine>
Specialized casting sand removal equipment
High-speed vibration casting sand removal equipment
Specialized cutting equipment
Flexible-type finishing equipment for FC casting work
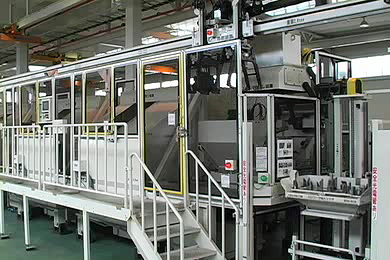
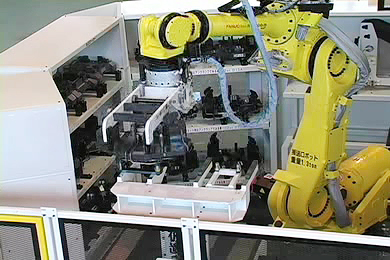
<Equipment component example>
・Sand Removal Equipment
・No.1 Deburring Machine /No.2 Deburring Machine
・Palette change system
Beer & Liquid Related
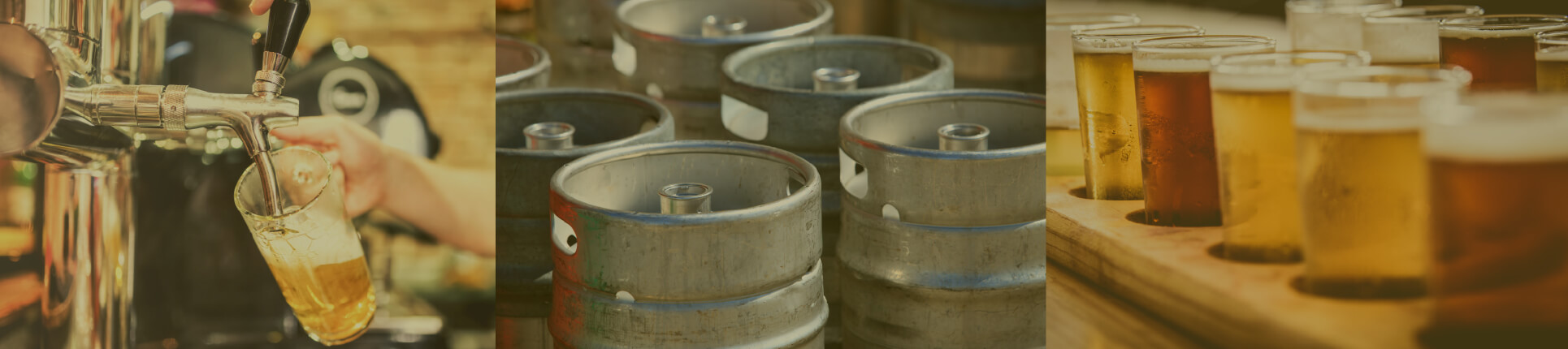
Simple keg washing equipment
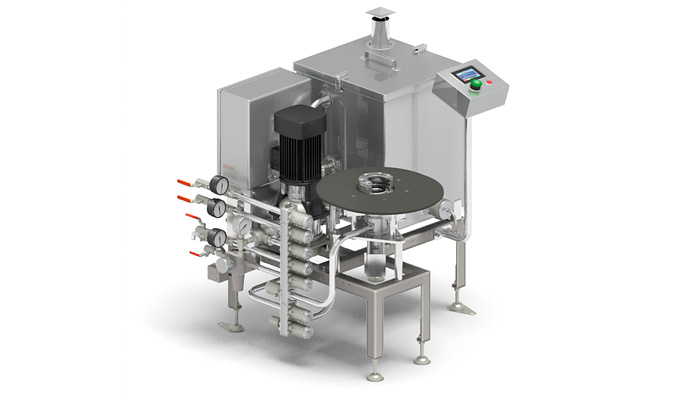
We offer keg washers designed for craft breweries and mini breweries. This dedicated keg washer is space-efficient and compatible with all keg types.
Features
- Standard compatibility with currently distributed keg sizes (10L to 25L class). For other sizes, please consult with us.
- Operation settings can be adjusted according to the keg type.
- Capable of CO2 pressurization (filling preparation) after washing is completed.
- Achieves a washing time of approximately 100 seconds, significantly improving work efficiency compared to manual operations.
- Simple operation by just pressing the start button.
- The monitor section uses a graphic panel that is easy to see and operate.
- Maintenance, such as gasket replacement, is easy.
- Space-saving design, easy installation, and smooth startup at the customer’s facility.
- Comprehensive after-sales service. Since almost all parts are manufactured in-house, you can rest assured in the event of any repairs.
Small keg washing and filling equipment
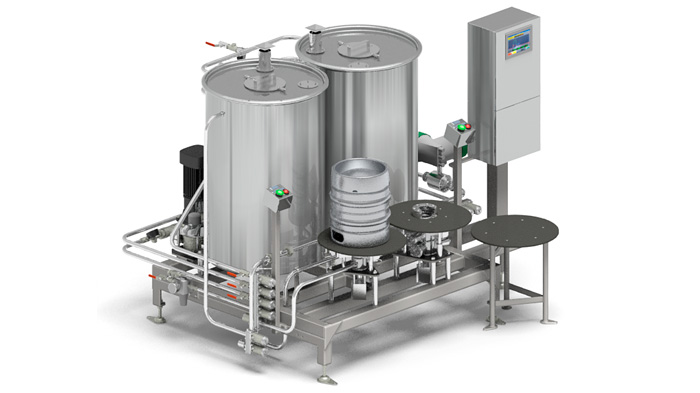
We offer a revolutionary keg washing and filling system for craft beer, incorporating our unique technology from Shiga Yamashita. It is space-efficient and high-performance, compatible with all keg types.
Features
- Standard compatibility with currently distributed keg sizes (10L to 25L class). For other sizes, please consult with us.
- Achieves high-precision filling to minimize beer loss to the utmost limit.
- Allows for fine-tuned operation settings according to keg type and liquid type.
- Achieves a washing time of approximately 80 seconds and a filling time of approximately 80 seconds, significantly improving work efficiency compared to manual operations.
- Standardly equipped with CIP (Clean-In-Place) functionality.
- Simple operation by just pressing the start button.
- The monitor section uses a graphic panel that is easy to see and operate.
- Maintenance, such as gasket replacement, is easy.
- Space-saving design, easy installation, and smooth startup at the customer’s facility.
- Comprehensive after-sales service. Since almost all parts are manufactured in-house, you can rest assured in the event of any repairs.
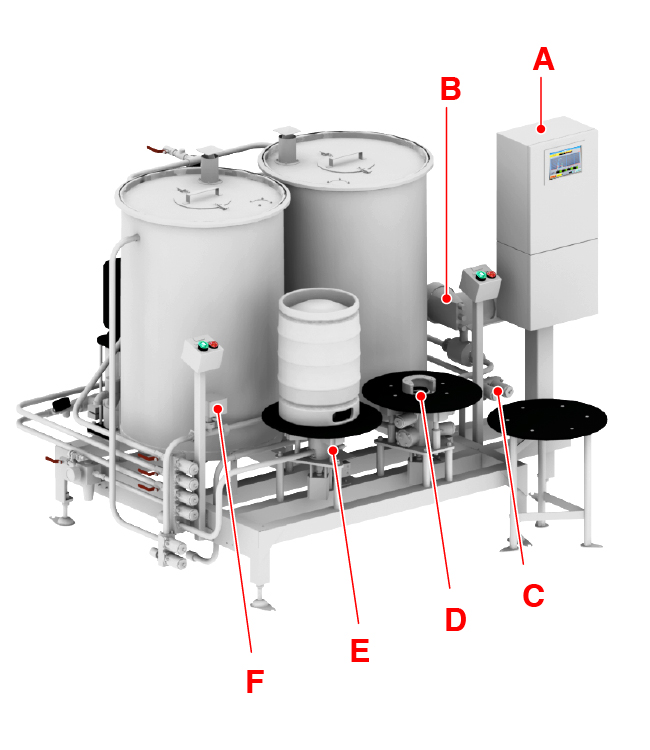
Operator can check and analyze past events using varieties of traceability function.
Liquid Flow Sensor trace flow rate graph which tells washing condition of the keg.
Remote-maintenance function enables to be checked and monitored from outside.
Sophisticated analyzing function helps inves-tigation for trouble cause.
Latest model of Electromagnetic Flow Meter is equipped and beer volume is automatic-ally set by keg size change.
Much less beer loss comparing ordinal Full-Fill system.
Simple structure and Easy maintenance.
Valve position can be seen and checked from outside.
Diaphragm type structure makes lifetime long-er by preventing seal damage caused from scale object.
Simple structure and Easy maintenance.
Washing & Filling Heads are kept clean due to no clamp cylinder unit above heads.
Due to new clamping structure which clamps directly to keg neck, more stable keg clamping is achieved comparing ordinal clamp system, especially for damaged kegs.
Simple and compact structure and Easy maintenance.
Smaller size diaphragm makes seal lifetime longer. especially for damaged kegs.
Monitoring by this sensor ensures sufficient washing and sterilization for the kegs.
Auto-Offset and Auto-gain function require no adjustment.
Longer lifetime is achieved due to stronger detection part.
Automatic keg conveying, washing and filling equipment
We offer a new automatic keg conveying, washing, and filling system. It can be customized to suit the scale and needs of your operation.
Rotary keg washing and filling equipment
A space-saving design for rotary washing and filling draft beer kegs.
Customizable to suit individual customer requirements.
Local manufacturing enables satisfying even higher quality requirements, and follow-up services are always close at hand.
Incorporates a variety of inspection mechanisms and sophisticated self-diagnostic functions.
BAG IN BOX
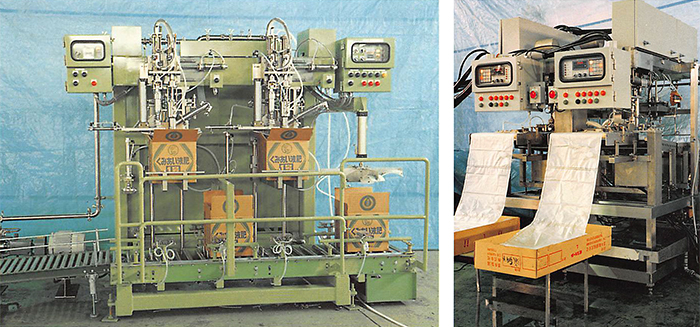
Equipment used to fill already boxed bags with liquid.
Designed and manufactured to suit the liquid used and the conditions of the installation.
Other Equipment
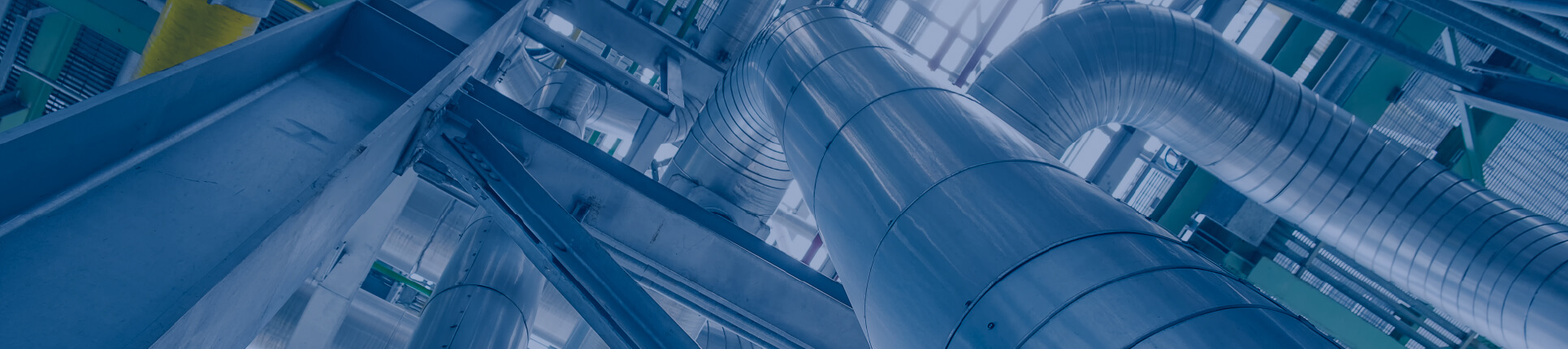
Soot extraction systems
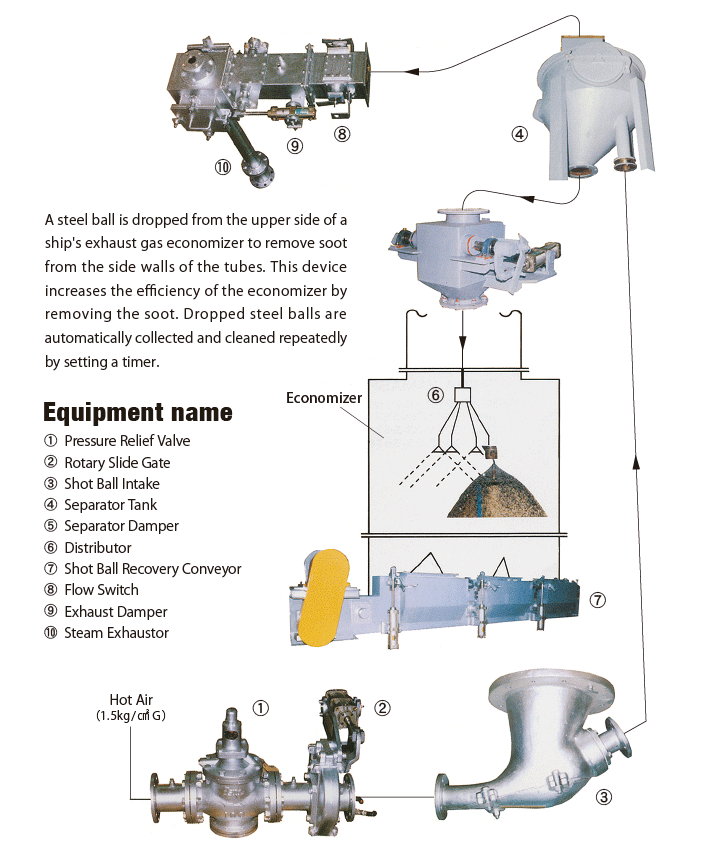
Pneumatic transportation equipment
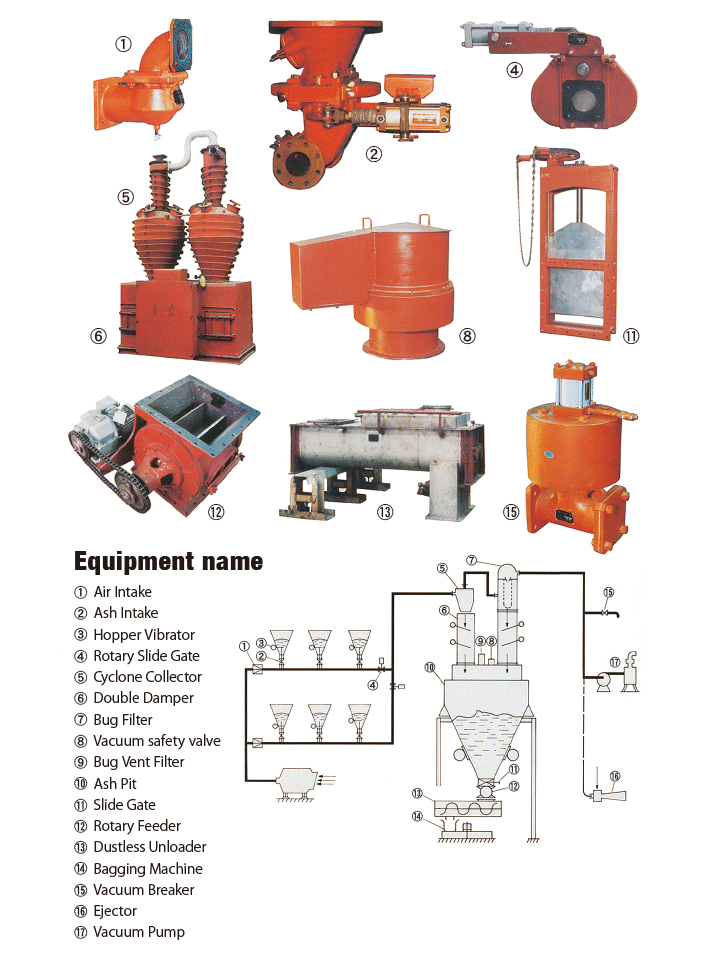
Urban refuse incineration and processing equipment
Equipment fitted to incineration and processing equipment.